MANUAL CHECK VALVES
MANUAL CHECK VALVES
Parker provides the industry’s widest selection of check valves, available in a variety of end connections. Our valves are used in a diverse range of applications, from air and fuel systems to load holding. Our check valves utilize a variety of media including oil, air, and water and are made from materials such as aluminum, stainless steel, brass, and carbon steel. Parker check valves employ economical metal seating or zero-leak seating, with elastomer seals using a custom-molded seat design.
MANUAL CHECK VALVES
Parker check valves are unidirectional flow control devices used primarily in hydraulic systems to eliminate potential damage caused by fluid back pressure.
DT Series Check Valves (up to 5,000 psi) have a metel to metal hard seat design with a one piece body and all steel construction. The body is a compact size with a variety of male port end configurations. These are in-line unidirectional valves with standard spring crack pressures of 1, 5, and 65 psi. The DT Series are available in a wide range of sizes for flow capacities up to 100 gpm.
Check valves are important components that are often overlooked when building a fluid system. A check valve can optimize system performance in the following ways:
• Ensure hydraulic fluid flows in only one direction
• Eliminate potential damage from back pressure
• Isolate sections of a system or system components
Basic check valve construction consists of a valve body with an inlet and an outlet port. Inside, a moveable poppet valve is controlled by spring pressure. In most cases the valve is normally closed, opening when the fluid pressure is greater than the spring force (crack pressure), thus allowing the fluid to flow in only one direction. When reverse flow attempts to enter though the outlet the poppet closes and flow through the valve is stopped.
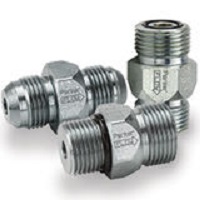
HARD SEAT IN-LINE CHECK VALVES (UP TO 5000 PSI) – COMPACT ONE PIECE BODY, MALE FITTING ENDS – DT SERIES
Hard seat check valves utilize a durable metal to metal seal to withstand high flow surges and provide longer service life.
Technical Characteristics:
• Sizes: 1/4” to 1-1/4”
• Material: Steel
• Inlet Port Ends: Male ORB, Male JIC, Male ORFS
• Outlet Port Ends: Male ORB, Male JIC, Male ORFS
• Optional crack pressures available from 1 to 200 psi in 5 psi increments
• Orificed valve option
• Custom shapes and configurations
Note: Some options may not be standard configurations. Please contact the Quick Coupling Division for availability and delivery.
Markets:
• Industrial
• Construction
• Agriculture
• Transportation
• MRO
Features/Benefits:
• Allows the fluid to flow in only one direction, protecting the system from fluid back pressure
• metal to metal hard seat provides longer life and is durable for high flow surges
• Custom shapes and configurations can integrate special features to reduce the number of components and potential leak points in a system
• Optional crack pressures are available on request
• Optional orificed valve allows metered flow when the valve is closed. Orifice bore size is determined by application requirements.
Applications:
• Industrial, mobile, and construction equipment
• Restrictor Check Circuit
• High/Low Pump Circuit
• Slow Advance/Rapid Return Circuit
• Oil Cooler By-Pass Circuit
• Sequence Circuit
• Pilot Pressure Circuit
• Accumulator Circuit
Parker’s C Series check valves are designed for uni-directional flow control of critical fluids and gases.
Parker’s C Series Check Valves are designed as a compact, inline check valve. These check valves provide uni-directional flow control of fluids and gases. To help prevent improper installation, all check valves have a flow arrow label with the valve’s crack pressure rating permanently attached. The availability of a wide range of seat materials provide the system designer a variety of uses over a standard, general purpose check valve.
Markets:
• Oil and Gas
• Pulp and paper
• Pharmaceutical
• Power
Features/ Benefits:
• Resilient, custom molded, blow-out resistant seat design
• Back stopped poppet minimizes spring stress
• 100% factory tested for both crack and reseat
• Cracking pressures include:
1/3, 1, 5, 10, 25, 50, 75, and 100 psi.
• Port connections include male and female NPT, CPI™, A-LOK®, UltraSeal, VacuSeal, BSP, SAE and Seal-Lok®
• Heat code traceability
Applications:
• Test Panels
• Back Flow Preventers
Parker’s swing type check valves are designed to protect low pressure air, liquid, or gas systems from fluid back pressure.
2600 Series Check Valves have a spring-loaded, trapdoor style valve. The valve opens when system pressure approaches 1/2 psi to permit full flow with low pressure drop. As system pressure is relieved, the valve closes, retaining fluids upstream.
These in-line check valves are designed with a low crack pressure spring especially for diesel and gasoline engine fuel lines. The 2600 Series are available in two sizes and can be used in low pressure air, liquid or gas systems.
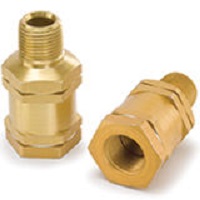
FUEL LINE CHECK VALVES – LOW PRESSURE (250 PSI), FULL FLOW SWING VALVE, LIGHTWEIGHT ALUMINUM – 2600 SERIES
Technical Characteristics:
• Sizes: 1/4”, 3/8”
• Material: Aluminum
• Port Ends: Male NPTF
Markets:
• Construction
• Mobile Equipment
• Truck
Features/Benefits:
• Lightweight corrosion resistant aluminum construction
• Swing style valve allows full flow with low pressure drop
• 1/2 psi maximum crack pressure for use in low pressure air, liquid, or gas systems
Applications:
• Diesel and gasoline engine fuel lines
• Externally mounted oil filters and coolers
• Transmission fluid lubrication lines
Parker’s high performance non-return valves can offer the user a cold working pressure rating up to 10,000 psi/689 bar maximum, with a cracking pressure of 10 psi maximum.
Parker’s Hi Check series high performance non-return valves are designed for unidirectional flow control of fluids and gases in process instrumentation applications. There is a choice of two check valve models, with cold working pressures of 10000 PSI (689 bar) and 6000 PSI (414 bar). Both check valves have an opening (or ‘cracking’) pressure of 10 PSI (0.7 bar). These robust check valves feature a two-piece metal seated body design to minimise any risk of leakage. The Parker check valves are available with a choice of integral male or female NPT, or single- or two-ferrule compression style ends, the compression ends enable users to eliminate the use of taper threads and thread sealant – further reducing the number of potential leakage paths and avoiding system contamination problems. There is a comprehensive range of inlet and outlet connections, covering imperial sizes of 1/4″, 3/8” and 1/2″, and metric sizes of 6 mm, 10 mm and 12 mm. The check valves are designed to meet the pressure and temperature requirements of ANSI/ASME B.16.34, as limited by the seat materials. NACE compliant versions are available. As standard, Hi Check valves are manufactured from 316 stainless steel, with duplex and monel versions optionally available. For maximum applications flexibility, there is an extensive choice of O-ring materials, including FPM75 and V1238-95 fluorocarbon rubber, Buna-N, ethylene propylene rubber and highly fluorinated fluorocarbon rubber.
Markets:
• Oil and Gas Offshore
• Oil and Gas Onshore
• Petrochemical
• Chemical
• Power Generation
Features/Benefits:
• ANSI/ASME B.16.34
• Heat code traceable
Applications:
• Lubrication skids
• Water Treatment
• Chemical injection skids
• Hydraulic systems for wellhead control
• Emergency shut down
• Pumping packages
• Gas booster systems
• Test equipment
Parker’s CO Series check valves are designed for uni-directional flow control of critical fluids and gases in industries such as pharmaceutical,research and microelectronics.
Parker’s CO Series Check Valves are designed for high integrity, leak proof systems with uni-directional flow control of critical fluids and gases up to 6,000 PSI (414 BAR). These inline check valves are suitable for instrumentation applications requiring high integrity leak rates and re-sealing capabilities.
Markets:
• Microelectronics
• Research
• Chemical Processing
• Pharmaceutical
Features/Benefits:
• Seal integrity across the seat and to atmosphere is tested to 4 x 10-9 std atm-cc/sec (4 x 10-10 kPa – L/sec) for the CO4L with fluorocarbon rubber seals. All other sizes and seal materials are tested to 1 x 10-5 std tm-cc/sec (1 x 10-6 kPa – L/sec).
• Special seat seal design provides a repeatable high integrity seal and accurate cracking pressures
• 100% factory tested. Cracking pressures include:
• 1/3, 1, 5, 10, 25, 50, 75, and 100 psi.
• Valves are available with male and female NPT, CPI™, A-LOK®, UltraSeal, male and female VacuSeal, and Tube Adapter ends
• Heat code traceability
• Color coded identification labels indicate seal material
Applications:
• Fill systems
• Back Flow Preventers
Parker check valves are unidirectional flow control devices used primarily in hydraulic systems to eliminate potential damage caused by fluid back pressure.
DC Series Check Valves (up to 3,000 psi) have a metel to metal hard seat design with a one piece body and all steel construction. Both inlet and outlet ports have female end fittings. These are in-line unidirectional valves with standard spring crack pressures of 1, 5, and 65 psi. The DC Series have low pressure drop and are available in a wide range of sizes up to 2″” and flow capacities to 300 gpm.
Check valves are important components that are often overlooked when building a fluid system. A check valve can optimize system performance in the following ways:
• Ensure hydraulic fluid flows in only one direction
• Eliminate potential damage from back pressure
• Isolate sections of a system or system components
Basic check valve construction consists of a valve body with an inlet and an outlet port. Inside, a moveable poppet valve is controlled by spring pressure. In most cases the valve is normally closed, opening when the fluid pressure is greater than the spring force (crack pressure), thus allowing the fluid to flow in only one direction. When reverse flow attempts to enter though the outlet the poppet closes and flow through the valve is stopped.
Hard seat check valves utilize a durable metal to metal seal to withstand high flow surges and provide longer service life.
Technical Characteristics:
• Sizes: 1/4” to 2″”
• Material: Steel
• Inlet Port Ends: Female NPSF, Female UNF, Female NPTF, Female UN
• Outlet Port Ends: Female NPSF, Female UNF, Female NPTF, Female UN
• Optional crack pressures available from 1 to 200 psi in 5 psi increments
• Orificed valve option
• Custom shapes and configurations
Note: Some options may not be standard configurations. Please contact the Quick Coupling Division for availability and delivery.
Markets:
• Industrial
• Construction
• Agriculture
• Transportation
• MRO
Features/Benefits:
• Allows the fluid to flow in only one direction, protecting the system from fluid back pressure
• Low pressure drop
• metal to metal hard seat provides longer life and is durable for high flow surges
• Custom shapes and configurations can integrate special features to reduce the number of components and potential leak points in a system
• Optional crack pressures are available on request
• Optional orificed valve allows metered flow when the valve is closed. Orifice bore size is determined by application requirements.
Applications:
• Industrial, mobile, and construction equipment
• Restrictor Check Circuit
• High/Low Pump Circuit
• Slow Advance/Rapid Return Circuit
• Oil Cooler By-Pass Circuit
• Sequence Circuit
• Pilot Pressure Circuit
• Accumulator Circuit
Parker check valves are unidirectional flow control devices used primarily in hydraulic systems to eliminate potential damage caused by fluid back pressure.
CPIFF Series Check Valves (5,000 psi) are soft seat, zero leakage poppet check valves with compact one piece construction. Standard crack pressures are 5, 15, 25, and 65 psi. These valves are available in a wide range of sizes up to 1″”, with female fitting ends and flow capacities up to 30 gpm.
Check valves are important components that are often overlooked when building a fluid system. A check valve can optimize system performance in the following ways:
• Ensure hydraulic fluid flows in only one direction
• Eliminate potential damage from back pressure
• Isolate sections of a system or system components
Basic check valve construction consists of a valve body with an inlet and an outlet port. Inside, a moveable poppet valve is controlled by spring pressure. In most cases the valve is normally closed, opening when the fluid pressure is greater than the spring force (crack pressure), thus allowing the fluid to flow in only one direction. When reverse flow attempts to enter though the outlet the poppet closes and flow through the valve is stopped.
Soft seat check valves have an O-ring or similar elastomeric seal between the poppet and body for improved leak resistance. The soft seat design is most compatible with “”clean” systems and is not indented for use in systems that have high surge flow. The seal material dictates the temperature range of the valve.
Technical Characteristics:
• Sizes: 1/4” to 1”
• Materials: Steel, Brass
• Seal Material: Fluorocarbon
• Standard Crack Pressures (psi): 5, 15, 25, and 65
• Port Ends: Female NPSF, Female SAE, Female British Parallel BS 2779
• Optional crack pressures available
• Orificed valve option
• Custom shapes and configurations
Note: Some options may not be standard configurations. Please contact the Quick Coupling Division for availability and delivery.
Markets:
• Industrial
• Construction
• Agriculture
• Transportation
• MRO
Features/Benefits:
• Allows the fluid to flow in only one direction, protecting the system from fluid back pressure
• Soft seated valve creates a leak free seal
• Fluorocarbon seal is standard
• Optional crack pressures are available on request
• Optional orificed valve allows metered flow when the valve is closed. Orifice bore size is determined by application requirements.
• Custom shapes and configurations can integrate special features to reduce the number of components and potential leak points in a system
Applications:
• Industrial, mobile, and construction equipment
• Restrictor Check Circuit
• High/Low Pump Circuit
• Slow Advance/Rapid Return Circuit
• Oil Cooler By-Pass Circuit
• Sequence Circuit
• Pilot Pressure Circuit
• Accumulator Circuit
Parker check valves are unidirectional flow control devices used primarily in hydraulic systems to eliminate potential damage caused by fluid back pressure.
CV Series Check Valves (3,000) psi are in-line unidirectional valves that have a two piece modular design. The larger body results in less pressure drop and increased performance. These check valves have standard spring crack pressures of 5 and 65 psi. The CV Series are available in a range of sizes up to 1″” and flow capacities to 100 gpm.
Check valves are important components that are often overlooked when building a fluid system. A check valve can optimize system performance in the following ways:
• Ensure hydraulic fluid flows in only one direction
• Eliminate potential damage from back pressure
• Isolate sections of a system or system components
Basic check valve construction consists of a valve body with an inlet and an outlet port. Inside, a moveable poppet valve is controlled by spring pressure. In most cases the valve is normally closed, opening when the fluid pressure is greater than the spring force (crack pressure), thus allowing the fluid to flow in only one direction. When reverse flow attempts to enter though the outlet the poppet closes and flow through the valve is stopped.
Hard seat check valves utilize a durable metal to metal seal to withstand high flow surges and provide longer service life.
Technical Characteristics:
• Sizes: 1/4”to 1″”
• Material: Steel
• Inlet Port Ends: Male UNF, Male UN
• Outlet Port Ends: Male UNF, Male UN, Male UNS
• Fitting Styles: Male Flare Inlet to Male Flare Outlet, Male O-Ring Boss Inlet to Male Seal-Lok Outlet
• Fitting O-ring Material: Nitrile
• Optional crack pressures available
• Orificed valve option
• Custom shapes and configurations
Note: Some options may not be standard configurations. Please contact the Quick Coupling Division for availability and delivery.
Markets:
• Industrial
• Construction
• Agriculture
• Transportation
• MRO
Features/Benefits:
• Allows the fluid to flow in only one direction, protecting the system from fluid back pressure
• All steel construction
• Low pressure drop for increased performance
• Poppet valve is heat treated to help prevent galling and damage from shocks and surges
• Optional crack pressures are available on request
• Optional orificed valve allows metered flow when the valve is closed. Orifice bore size is determined by application requirements.
• Custom shapes and configurations can integrate special features to reduce the number of components and potential leak points in a system
Applications:
• Industrial, mobile, and construction equipment
• Restrictor Check Circuit
• High/Low Pump Circuit
• Slow Advance/Rapid Return Circuit
• Oil Cooler By-Pass Circuit
• Sequence Circuit
• Pilot Pressure Circuit
• Accumulator Circuit
Parker check valves are unidirectional flow control devices used primarily in hydraulic systems to eliminate potential damage caused by fluid back pressure.
S6C and 3C Series Check Valves (up to 6,000 psi) are soft seat, zero leakage poppet check valves with a two piece construction. The two piece construction allows for a variety of end fitting combinations.
These check valves have various standard crack pressures and flow rates up to 175 gpm. The S6C & 3C Series valves are available in a range of sizes and steel or stainless steel materials for flow capacities up to 175 gpm.
Check valves are important components that are often overlooked when building a fluid system. A check valve can optimize system performance in the following ways:
• Ensure hydraulic fluid flows in only one direction
• Eliminate potential damage from back pressure
• Isolate sections of a system or system components
Basic check valve construction consists of a valve body with an inlet and an outlet port. Inside, a moveable poppet valve is controlled by spring pressure. In most cases the valve is normally closed, opening when the fluid pressure is greater than the spring force (crack pressure), thus allowing the fluid to flow in only one direction. When reverse flow attempts to enter though the outlet the poppet closes and flow through the valve is stopped.
Soft seat check valves have an O-ring or similar elastomeric seal between the poppet and body for improved leak resistance. The soft seat design is most compatible with “”clean” systems and is not indented for use in systems that have high surge flow. The seal material dictates the temperature range of the valve.
Technical Characteristics:
• Sizes: 1/4”to 2”
• Materials: Steel, Stainless Steel, Brass
• Seal Material: Fluorocarbon
• Standard Crack Pressures (psi): 5, 15, 25, 65
• Inlet Port Ends: Male NPT, Male 37 degree flare, Male Face Seal, Female NPTF, Female SAE, Female British Parallel BS 2779
• Outlet Port Ends: Male NPT, Female NPTF, Female SAE, Male SAE 37 degree Flare, Male Face Seal, Female British Parallel BS 2779
• Optional crack pressures available
• Orificed valve option
• Custom shapes and configurations
Note: Some options may not be standard configurations. Please contact the Quick Coupling Division for availability and delivery.
Markets:
• Industrial
• Construction
• Agriculture
• Transportation
• MRO
Features/Benefits:
• Allows the fluid to flow in only one direction, protecting the system from fluid back pressure
• Soft seated valve creates a leak free seal
• Fluorocarbon seal is standard
• Optional crack pressures are available on request
• Optional orificed valve allows metered flow when the valve is closed. Orifice bore size is determined by application requirements.
• Custom shapes and configurations can integrate special features to reduce the number of components and potential leak points in a system
Applications:
• Industrial, mobile, and construction equipment
• Restrictor Check Circuit
• High/Low Pump Circuit
• Slow Advance/Rapid Return Circuit
• Oil Cooler By-Pass Circuit
• Sequence Circuit
• Pilot Pressure Circuit
• Accumulator Circuit
Parker’s LC-Series Lift Check Valves are a compact design and utilize a gravity assisted poppet to seal a wide variety of temperature extremes in instrumentation systems.
Parker’s LC-Series Lift Check Valve has been designed for a wide variety of temperature extremes from -100⁰F to 900⁰F (-148⁰C to 482⁰C). To achieve this performance, the check valve must be mounted in the proper orientation as the bonnet nut is clearly marked. In contrast to a general purpose lift check valve, the LC-Series has been designed to prevent flow in the reverse direction to within 99.9% of forward flow. This is ideal for liquid service applications. The gravity assisted poppet uses back pressure to achieve a seal.
Many industrial valves of this type require additional fittings (adapters) when connecting to tubing system. The LC Series does not require adapters and offers both single ferrule and two ferrule compression end connection integral to the valve body
Markets:
• Chemical
• Power
• Petrochemical
• Oil & Gas
• Research
Features/benefits:
• Wide temperature range
• Variety of end connections available
• Compact design
• Rugged, forged body construction
• 316 Stainless Steel construction
Applications:
• Back Flow Preventers
• Test Panels
• High Temperature Fill Systems
Parker’s CB Series check and filter check valves are a unique ball check design. These check valves handle uni-directional flow control of critical fluids and gases, especially in high temperature or “sticky” applications.
Parker’s CB and CBF Series Check Valves are designed for uni-directional flow control of fluids and gases. The unique floating ball valve design handles demanding services in a variety of industries. The CB/CBF Series are specifically designed to reduce check valve maintenance and performance requirements on dual fuel turbines. General poppet design check valves do not handle these high demand applications very well. Specific issues of a poppet check valve include, but are not limited to seat leakage, coking, high repair and maintenance costs. All of these issues directly affect turbine efficiency, impacting operating costs.
The advanced seat materials of the CB/CBF Series Check Valves are particularly suited for higher temperature applications requiring high integrity leak rates and re-sealing capabilities.
Markets:
• Power
• Chemical
• Oil & Gas
Features/benefits:
• Rugged and reliable floating ball valve seat design optimizes sealing characteristics while minimizing effects of coking.
• Optional hard PTFE coated ball cage resists poppet “stick” commonly experienced with fuel oil coking.
• Fully field serviceable with Parker rebuild kits. Replace seats in minutes without special tools.
• Advanced reinforced PTFE copolymer seat materials designed by Parker for demanding applications such as air purge and fuel oil.
• Integral “last chance” filter option for seat and nozzle protection.
• Connects directly to Parker metal hoses to assist in even further reduce turbine downtime during repairs.
Applications:
• Dual Fuel Turbines
• Fuel Systems
• High Temperature System Protection
• Injection Systems
Parker’s MAC Series (Ball and O-Ring) Check Valves provide unidirectional flow and shut-off for liquids and gases in medium pressure systems up to 15,000 PSI. These check valves utilize integral MPI Tube Fittings for a secure connection.
Parker’s MAC Series MPI Check Valves offer distinct designs over general check valves found in the market today. First, they are capable of working pressures up to 15,000 PSI. Then they are available as a ball check valve and the other is an o-ring check valve depending on the user’s design preference. Parker’s MACBL series (Ball Check Valve) prevent reverse flow where leak-tight shut-off is not mandatory. When differential drops below cracking pressure, valve closes. With all-metal components, valve can be used up to 650°F (343°C). Ball and poppet are an integral design to assure positive, in-line seating without “chatter”. Poppet is designed essentially for axial flow with minimum pressure drop.
Parker’s MACL series (O-Ring Check Valve) provides unidirectional flow and tight shut-off for liquids and gases with high reliability. When differential drops below cracking pressure*, valve shuts off. (Not for use as a Relief Valve)
Markets:
• Chemical
• Oil and Gas
• Refineries
• Power
Features/Benefits:
• Ball and O-Ring designs
• Ball Check is all metal and can reach up to 650F
• Low pressure drop
• MPI end connections
• Heat code traceability
• Variety of o-rings available for system flexibility
Applications:
• Process Control Lines
• Instrument Panels
• System Pressure Protection
Parker Bestobell’s cryogenic lift and swing check valves are designed with a loose flange bolted bonnet design that allows for thermal expansion and contraction and eliminates leakage, therefore enhancing safety.
Parker Bestobell’s range of cryogenic lift check and swing check valves feature an innovative loose flange bolted bonnet design that allows for thermal expansion and contraction, therefore eliminating leakage.
Available in Stainless Steel and Bronze, Parker Bestobell’s check valves are fitted with a swing return, allowing for use in any position. The PTFE seal incorporated into the valve disc ensures a drop tight shut off at ambient temperatures. With the swing check valve, wide openings also allow high flow rates at low-pressure drops.
Standardised parts are used in Parker Bestobell’s swing valves, globe, ball and gate valves. Parker Bestobell’s lift check valves are often specified in conjunction with globe valves and swing check valves would be used in conjunction with gate or ball valves.
The lift check valves feature a cone seat design for zero leak shut off, therefore maximising safety and performance.
Markets:
Industrial Gas
Features / Benefits:
• Unique Parker Bestobell loose flange bolted bonnet design allows for thermal expansion and contraction and eliminates leakage at the bonnet gasket.
• PTFE seal to ensure tight shut off at all times, enhancing safety.
• Quick and easy maintenance of PTFE components
Applications:
• Transport
• Storage
• Defence
• Processing
Liquid / Gas Type:
• Oxygen (O2)
• Nitrogen (N2)
• Argon (Ar)
• Carbon Dioxide (CO2)
• Krypton (Kr)
• Neon (Ne)
• Hydrogen (H2)
• Nitrous Oxide (N2O)
• Sulphur Hexafluoride (SF6)
• Natural Gas (CH4)
• Ethylene (C2H4)
• Trifluoromethane (CHF3)
The Parker Bestobell Automatic Sensing Pressure Reversing Obturator (ASPRO) is a concept that addresses the issue of back contamination from high-pressure carbon dioxide cylinders removing the opportunity for gas contamination.
This is a particular problem in the food and beverage industry, where on numerous occasions, contamination has occurred leading to product recalls and brand damage. There are also a growing number of applications in pharmaceutical production and clean process used in industrial production. The ASPRO was developed for the prevention of back contamination of CO2 from a high-pressure cylinder, or dewer to the main flow stream, preventing back flow pressures up to 3600 psi (250 bar), in accordance with recommendations requested by EIGA and BCGA. The flow co-efficient (CV) allows full flow of media from filling stations and portable delivery systems therefore no delay in filling time.
Markets:
Food and Beverage
Pharmaceutical
Features / Benefits:
• Fully automatic: no operator involvement required to operate the valve
• Designed for single point filling lines
• Designed and engineered for use with Group 1 gases
• Designed and manufactured in accordance with ASTM B31.1, BS EN 1626 and BS ISO 21011
Applications:
• CO2 bottling
Parker Conflow’s Code 11 is a check valve that is used in water dust suppression systems that keeps the pipelines “charged” with water so that the spray heads energise instantaneously when the supply valve is turned on.
Parker Conflow’s Code 11 is a check valve that is used in water dust suppression systems on mining cutting machines to keep the pipelines “charged” with water so that the spray heads energise instantaneously when the supply valve is turned on.
It is fitted into pipelines on systems where the flow of fluid is required in one direction only. The design is such that only the weight of the valve component needs to be overcome in the direction of fluid flow and hence the resistance across the unit is small. If system requirements necessitate the valve to be fitted vertically, then a light spring can be added.
The valve is suitable for both hydraulic and pneumatic systems and is designed especially for silent operation on equipment with pulsating or reverberating action (e.g. air compressors).
Available in 1/2″, 1″, 2″, 3″ & 4″ sizes and to a maximum working pressure of 125 bar.
The 1/2″ to 2″ sizes are of Brass construction and 2″ to 4″ sizes of Steel construction.
Markets:
• Quarrying
• Mining
• Air compressors – hydraulic or pneumatic systems.
Features/Benefits:
• Robust material.
• Allows flow in one direction only.
• Suitable for use with air, water or oil.
• Enables silent operation when used on equipment with pulsating or reverberating action.
Applications:
• Water dust suppression systems .
• Keeps pipelines supplied with water.
• Spray head is energised instantaneously next time supplied switched on.
Parker Conflow’s Code 103 is a pressure check valve range that enables individual checks of hydraulic pressure on each leg and ram on powered roof supports of coal faces.
Parker Conflow’s Code 103 range are pressure check valves for use in underground mining that is safe and without open-end, which potentially prevents damage to gauges when regular checking is required.
Code 103 range enables the monitoring of hydraulic pressure on the leg and ram on powered roof supports of coal faces with the ability to screw it directly into each roof support leg. Three different connection types are available to suit individual applications, for added flexibility.
The action of screwing the adaptor into the Code 103M pressure check valve, causes a probe to push the valve ball off its seat and allows system fluid to enter the pressure gauge to register a pressure reading.
The Conflow Code 103NS and NSA Pressure Check Valve swivel adaptors are used in conjunction with a pressure gauge to enable readings to be taken at the tapping point.
Unscrewing the adaptor allows the ball to reseat, thus isolating the system from the gauge again. A one-way valve, Code 103 ensures that fluid cannot run back, for added safety.
Code 103 has a 3/8″ BSP fitting and operates to a maximum working pressure of 690 bar.
Markets:
• Mining
Features/Benefits:
• Safe and secure method of pressure checking.
• Enables periodical checks of on-line pressure without the need for fixed gauges.
• No interruption of the normal circuit.
• Cost efficient method.
• Direct, quick connection to check pressure.
• Enables periodical checks without interruption to normal services.
Applications:
• Checking hydraulic pressure on each leg and ram on powered roof supports on coal faces
• Invaluable on applications where permanent gauges could be damaged.
Parker Conflow’s Code 1431 is an inline check value that permits movement of flow media, oil, water or air in one direction only in water dust suppression systems on mining cutting machines.
Parker Conflow’s Code 1431 is an inline check valve, which permits movement of flow media in one direction only in water dust suppression systems on mining cutting machines to keep the pipelines “charged” with water. It helps to prevent backflow of fluid media and operates with air, water and oil.
A light spring is fitted to assist with closure at low pressure differentials across the valve. This in-line valve fits neatly into a pipeline with minimum obstruction. It may be used horizontally or vertically.
Code 1431 is available in 3/8″, 1/2″, 3/4″ and 1″ sizes and with maximum working pressure of 275 bar.
Markets:
• Quarrying
• Mining
Features/Benefits:
• Spring assisted closure
• Stainless Steel Construction
• Low Pressure units available
• For use with oil, water and air.
• Extremely compact as in-line valve
• Reduces risk of damage.
• Robust and low maintenance.
Applications:
• Water dust suppression systems on cutting machines for mining and quarrying.